In the realm of bottling, the automatic double head bottle gripping capping machine has emerged as a revolutionary piece of equipment, transforming the way products are packaged. Here are the key factors that make it a game – changer.
Table of Contents
1. Unprecedented Speed and Efficiency
Dual – Head Operation
The most obvious advantage is its double – head design. While traditional single – head capping machines work on one bottle at a time, the automatic double head bottle gripping capping machine can cap two bottles simultaneously. This means that in the same amount of time, it can produce double the output. For example, in a large – scale beverage bottling plant that needs to meet high – volume orders, this increased speed can significantly reduce production time. A single – head machine might cap 80 bottles per minute, while a double – head machine can reach 160 bottles per minute, enabling companies to fulfill orders faster and keep up with market demand.
Continuous Flow and Minimized Downtime
These machines are engineered for seamless, continuous operation. They are equipped with advanced sensors and control systems that can quickly detect any issues during the capping process, such as misaligned caps or bottles. Once a problem is detected, the machine can make immediate adjustments without shutting down the entire production line. This reduces the amount of time wasted on troubleshooting and restarts, ensuring a smooth and uninterrupted flow of bottles through the capping stage.
2. Superior Capping Quality
Precise Bottle Gripping
The automatic double head bottle gripping capping machine uses specialized grippers to hold the bottles firmly in place. These grippers are designed to adapt to different bottle shapes and sizes, from small perfume vials to large industrial containers. By securely gripping the bottles, the machine can apply the capping force accurately, ensuring a tight and consistent seal. This is crucial for maintaining product integrity, as a loose or uneven cap can lead to leakage, spoilage, and a negative customer experience.
Consistent Torque Application
Achieving the right amount of torque when capping is essential. Over – tightening can damage the bottle or cap, while under – tightening can result in a faulty seal. The double – head capping machine is equipped with sophisticated torque control systems. Operators can set the exact torque requirements for each type of cap and bottle combination, and the machine will apply that torque consistently across all bottles. This consistency in capping quality helps to build brand reputation and reduces the risk of product returns due to capping issues.
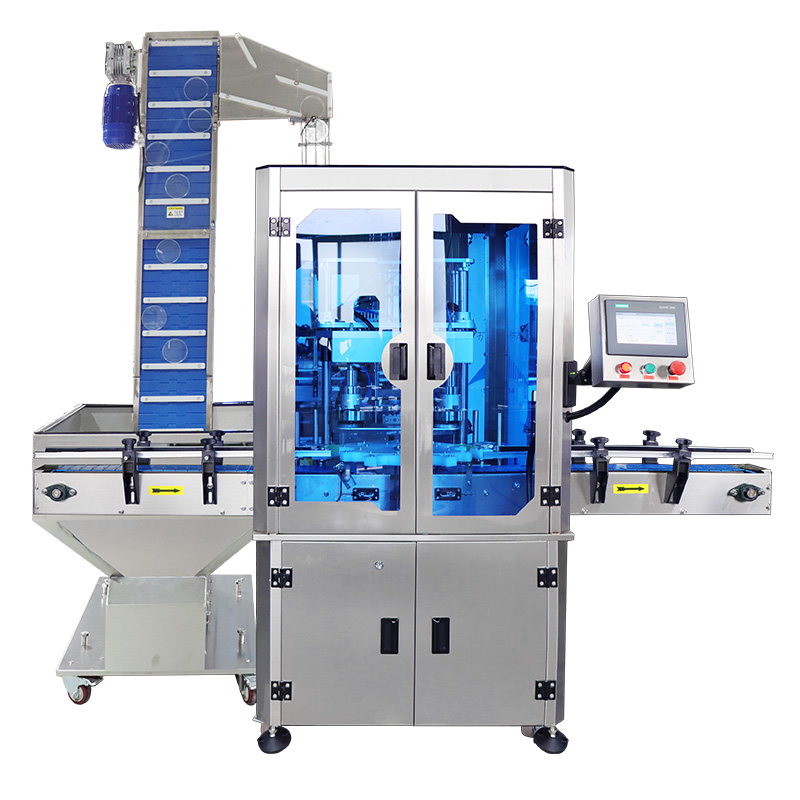
3. Enhanced Flexibility and Adaptability
Compatibility with Diverse Bottles and Caps
In the modern bottling industry, companies often produce a wide range of products in different bottle materials (glass, plastic, metal), shapes (round, square, oval), and sizes. The automatic double head bottle gripping capping machine is highly versatile and can handle various types of caps, including screw caps, snap – on caps, and corks. This flexibility allows bottling companies to use the same machine for multiple product lines, eliminating the need to invest in separate capping equipment for each product.
Quick Changeover
When switching between different bottle and cap configurations, the double – head capping machine can be reconfigured quickly. It features modular components and easy – to – use adjustment mechanisms that enable operators to make the necessary changes in a short amount of time. This is especially important in a dynamic market where consumer preferences change rapidly, and companies need to be able to adapt their product offerings quickly.
4. Cost – Effectiveness
Labor Savings
Automating the capping process with a double – head machine reduces the need for a large workforce. In a manual or semi – automated capping operation, multiple workers are required to handle the bottles, place the caps, and operate the capping equipment. With an automatic double head bottle gripping capping machine, much of this work is done by the machine itself, resulting in significant labor cost savings. These savings can be reinvested in other areas of the business, such as research and development or marketing.
Reduced Product Waste
The high – precision capping capabilities of the machine help to minimize product waste. Inaccurate capping can lead to a large number of rejected bottles, which means wasted raw materials, packaging, and labor. By ensuring consistent and reliable capping, the double – head machine reduces the number of defective products, saving on production costs and improving overall profitability.
In conclusion, the automatic double head bottle gripping capping machine offers a combination of speed, quality, flexibility, and cost – effectiveness that makes it a true game – changer in the bottling industry. It allows companies to increase their production capacity, improve product quality, adapt to market changes, and reduce costs, giving them a competitive edge in the marketplace.