La fuga es un problema común en el embalaje que puede comprometer seriamente la integridad y la calidad del producto. Sin embargo, máquinas de tapa de vacío automáticas ofrece una solución confiable a este desafío persistente.
La primera forma en que estas máquinas evitan fugas es a través de un sellado preciso. Aplican presión y calor constantes para crear un sello apretado y uniforme alrededor del borde del frasco de vidrio. Esto elimina los puntos o huecos débiles donde podría ocurrir fugas.
El proceso de vacío es otro aspecto crucial. Al eliminar el aire del interior del frasco, el diferencial de presión ayuda a mantener la tapa firmemente en su lugar. Esto reduce el riesgo de que la tapa aparezca o permita que las sustancias se filtre.
Las máquinas automáticas de tapa de vacío también incorporan mecanismos de control de calidad. Pueden detectar cualquier imperfección en el sello durante el proceso de limitación y alertar a los operadores o rechazar automáticamente contenedores defectuosos. Esto asegura que solo los frascos sellados correctamente a través de la línea de producción.
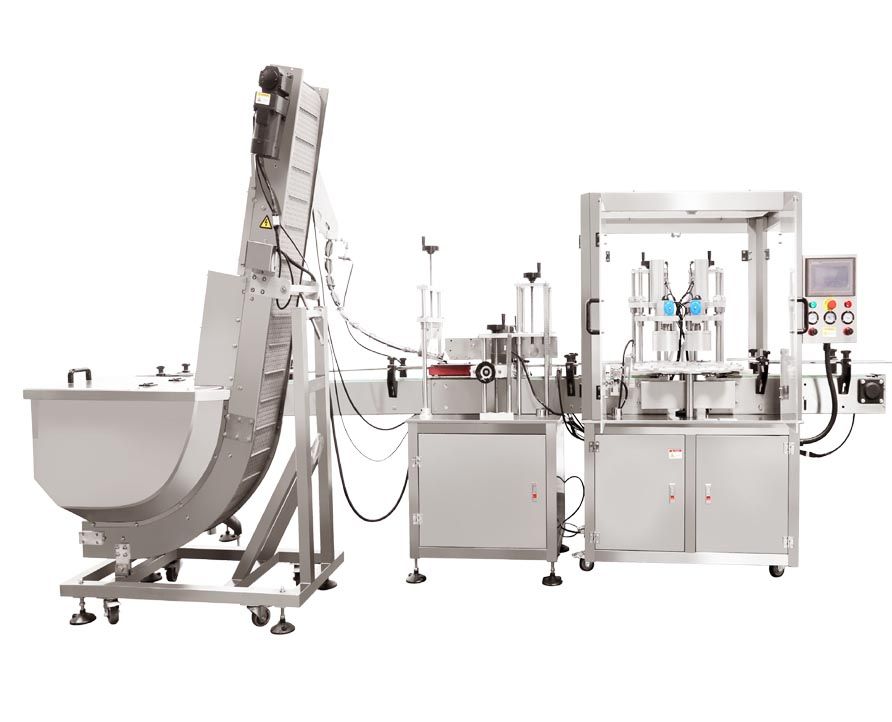
Los materiales utilizados para las tapas y los sellos se seleccionan por su durabilidad y compatibilidad con el proceso de limitación de vacío. Los materiales de alta calidad resisten el desgaste, la rotura y la deformación, mejorando aún más la integridad del sellado.
En conclusión, las máquinas automáticas de limitación de vacío juegan un papel vital en la resolución de problemas de fuga y protegen la integridad de los productos envasados, asegurando que lleguen al mercado en condiciones óptimas.
By combining these features, automatic vacuum capping machines provide a robust defense against leakage, safeguarding the product integrity from the moment of packaging until it reaches the consumer. This not only protects the quality of the contents but also enhances the reputation of the brand and customer satisfaction.
In conclusion, automatic vacuum capping machines play a vital role in solving leakage issues and protecting the integrity of packaged products, ensuring they reach the market in optimal condition.