Table of Contents
Introduction
In industries that handle powdered products, such as pharmaceuticals, food, and chemicals, consistent powder filling is of utmost importance. Inconsistent filling can lead to a range of issues, from product quality problems to regulatory non – compliance. Traditional filling methods often struggle to achieve the desired level of consistency. However, semi – automatic powder filling machines have emerged as a reliable solution to this long – standing problem.
The Problem of Inconsistent Filling
Manual Filling Drawbacks
Manual powder filling is highly susceptible to human error. Workers may vary in the amount of powder they dispense into each container due to factors like fatigue, lack of concentration, or differences in technique. For example, in a small – scale food production facility where spices are manually filled into packets, one worker might fill a packet slightly more generously than another, leading to inconsistent product weights and flavors.
Basic Automated Systems’ Limitations
Some basic automated filling systems also face challenges in achieving consistent filling. They may not be able to adapt well to variations in powder characteristics such as density, particle size, and flowability. For instance, if the powder becomes more compacted over time, an automated system that is not properly calibrated may under – fill containers.
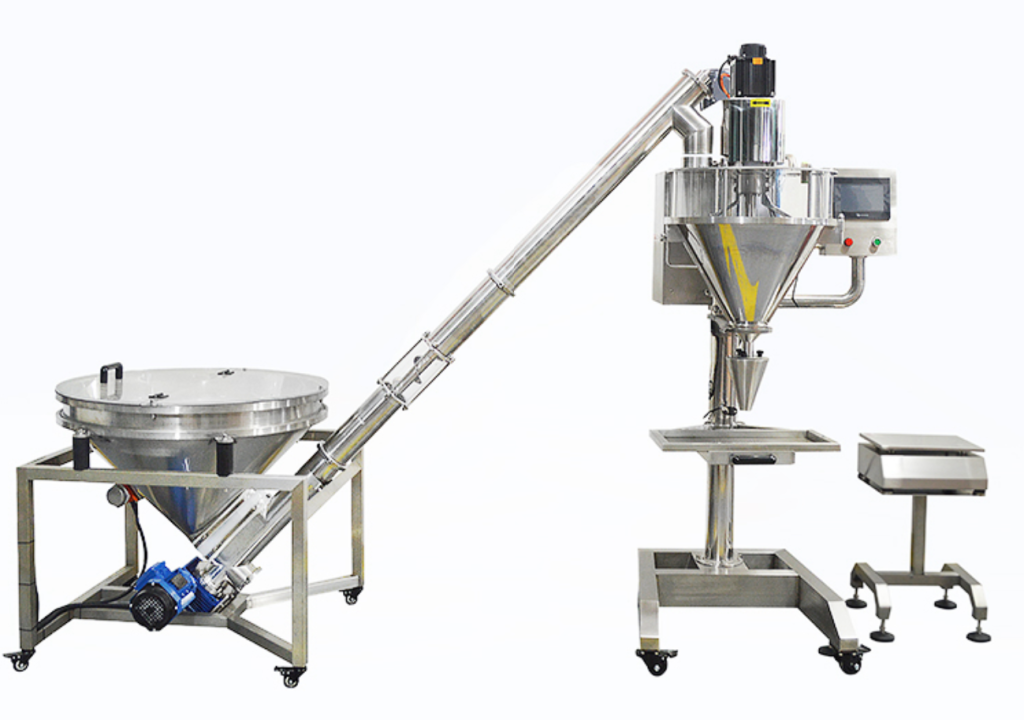
How Semi – Automatic Machines Address Inconsistency
Precise Dosing Mechanisms
Semi – automatic powder filling machines are equipped with advanced dosing systems. These systems can be precisely calibrated to measure and dispense a specific amount of powder into each container. For example, in the pharmaceutical industry, where accurate dosages are critical, these machines can use volumetric or gravimetric dosing methods. Volumetric dosing measures the volume of powder, while gravimetric dosing weighs the powder, ensuring that each pill capsule or sachet contains the exact amount of the active ingredient.
Adaptability to Powder Variations
One of the key advantages of semi – automatic machines is their ability to adapt to different powder properties. They can be adjusted to account for changes in powder density, humidity, and particle size. For example, if a food manufacturer is filling a new type of flour with different flow characteristics, the semi – automatic machine can be fine – tuned to ensure consistent filling. This adaptability is achieved through features such as adjustable filling speeds, auger rotations, and vibration settings.
Operator Intervention for Quality Control
While semi – automatic machines are automated to a certain extent, they still allow for operator intervention. Operators can monitor the filling process in real – time and make adjustments as needed. For instance, if they notice that the filling amount is starting to deviate slightly, they can quickly recalibrate the machine or check for any blockages in the powder delivery system. This human – machine interaction helps to maintain a high level of consistency throughout the production run.
Benefits of Consistent Filling with Semi – Automatic Machines
Improved Product Quality
Consistent filling directly translates to improved product quality. In the pharmaceutical industry, accurate dosing ensures the effectiveness and safety of medications. In the food industry, consistent filling of products like coffee or powdered drinks guarantees a uniform taste and experience for consumers. This, in turn, enhances brand reputation and customer satisfaction.
Regulatory Compliance
Many industries are subject to strict regulatory requirements regarding product quantity and quality. Semi – automatic powder filling machines help companies meet these regulations by providing consistent filling. For example, pharmaceutical companies must adhere to FDA regulations regarding the accurate dosing of medications. By using semi – automatic machines, they can ensure that their products meet these standards and avoid costly fines and recalls.
Cost Savings
Consistent filling reduces waste. When containers are filled accurately, there is less over – filling, which means less product is wasted. This can lead to significant cost savings over time, especially for companies that produce large volumes of powdered products. Additionally, the reduced need for rework and quality control checks also contributes to cost – efficiency.
Conclusion
Semi – automatic powder filling machines offer an effective solution to the problem of inconsistent filling. Their precise dosing mechanisms, adaptability to powder variations, and the possibility of operator intervention make them a valuable asset in industries that rely on accurate powder filling. By improving product quality, ensuring regulatory compliance, and achieving cost savings, these machines are transforming the way powdered products are filled and produced.