In the highly competitive arena of manufacturing, finding that one element that can give a business an edge is crucial. Double head rotor pump filling machines have emerged as the secret weapon that many industries are leveraging to transform their operations and gain a significant advantage.
Table of Contents
Unveiling the Technology
At the core of these remarkable machines lies the rotor pump. A positive – displacement pump, the rotor pump operates through a set of rotors that rotate within a housing. As they turn, chambers are formed that trap and move the liquid from the inlet to the outlet. The “double head” aspect means there are two independent filling stations on the machine, enabling simultaneous filling of two containers.
Precision: The Key to Quality
In industries where product quality is non – negotiable, precision is king. Double head rotor pump filling machines offer an astonishing level of accuracy. For instance, in the pharmaceutical industry, where a slight deviation in dosage can have serious consequences, these machines ensure that each vial or syringe is filled with the exact amount of medication. The positive – displacement nature of the rotor pump allows for meticulous control of the flow rate, eliminating the risk of over – filling or under – filling. This precision not only guarantees product quality but also builds trust with consumers.
Speed: Meeting Market Demands
In today’s fast – paced world, speed is of the essence. Double head rotor pump filling machines are engineered for high – speed operation. With two filling heads working in tandem, they can double the filling rate compared to single – head machines. In a beverage bottling plant, a single – head machine might fill 60 bottles per minute, while a double head machine can effortlessly reach 120 bottles per minute. This increased throughput enables companies to meet large – scale market demands promptly, reducing lead times and enhancing customer satisfaction.
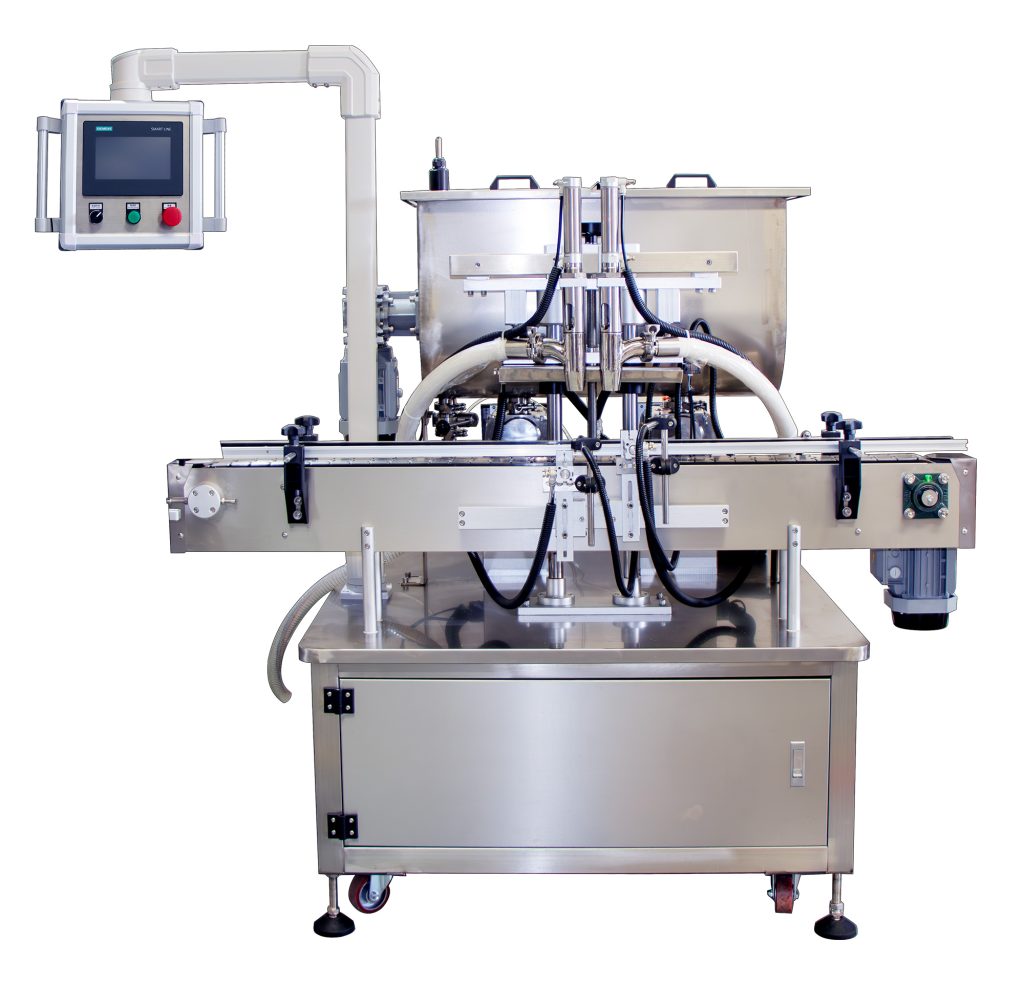
Versatility: A One – Machine Solution
One of the most remarkable features of double head rotor pump filling machines is their versatility. They can handle a vast array of liquids, regardless of their viscosity. Whether it’s a thin, free – flowing liquid like perfume or a thick, sticky substance such as honey, these machines can adapt. This means that a single machine can be used across multiple product lines within a manufacturing facility. For example, a food processing company can use the same machine to fill salad dressings, sauces, and jams, eliminating the need for multiple specialized filling machines.
Efficiency: Minimizing Waste and Downtime
Efficiency is not just about speed; it’s also about minimizing waste and downtime. Double head rotor pump filling machines are designed with this in mind. The precise filling reduces product waste, as there is less over – filling. Additionally, these machines are built to be reliable, with fewer moving parts that can break down. They often come equipped with self – cleaning and self – diagnostic features. The self – cleaning function prevents clogging, which can cause production stoppages, and the self – diagnostic system can detect potential issues early, allowing for timely maintenance.
Integration: Seamless Operation
To truly optimize production, all equipment in a manufacturing line must work together seamlessly. Double head rotor pump filling machines are designed for easy integration with other production equipment such as conveyors, cappers, and labelers. They can be synchronized with the conveyor system to ensure a continuous flow of containers. When a container is filled, the machine can communicate with the capper to initiate the next step in the process. This seamless integration eliminates bottlenecks and ensures a smooth and efficient production flow.
Conclusion
Double head rotor pump filling machines are indeed the secret weapon that many industries have been searching for. Their precision, speed, versatility, efficiency, and ease of integration make them an invaluable asset in modern manufacturing. By investing in these machines, companies can enhance their product quality, increase their production capacity, reduce costs, and gain a competitive edge in the market. As technology continues to evolve, these machines will likely become even more advanced, further solidifying their position as a game – changer in the world of filling operations.