Table of Contents
Introduction
Jam, a beloved spread enjoyed by people of all ages, has a long – standing tradition in the food industry. The packaging of jam in glass jars has always been an important part of its presentation and preservation. However, the introduction of the fully automatic jam glass jar vacuum capping machine has brought about a revolutionary change in the jam packaging process.
1. Enhanced Product Preservation
Vacuum Sealing Technology
The most significant feature of the fully automatic jam glass jar vacuum capping machine is its ability to create a vacuum inside the glass jar before sealing. Oxygen is the enemy of jam, as it can cause oxidation, leading to color changes, flavor degradation, and the growth of spoilage organisms. By removing the air from the jar, the machine creates an anaerobic environment. This slows down the chemical reactions that cause spoilage, extending the shelf – life of the jam. For example, a jar of jam sealed with a traditional method may last for a few months, while one sealed with a vacuum capping machine can remain fresh for up to a year or more.
Maintaining Nutritional Value
In addition to preserving flavor and appearance, the vacuum – sealing process helps to maintain the nutritional value of the jam. Many of the vitamins and antioxidants in fruits used to make jam are sensitive to oxygen. By reducing the oxygen exposure, the machine ensures that these nutrients are retained, providing consumers with a healthier product.
2. Increased Production Efficiency
High – Speed Operation
Traditional jam capping methods were often labor – intensive and time – consuming. Workers had to manually place caps on jars and then seal them, which was a slow and error – prone process. The fully automatic jam glass jar vacuum capping machine, on the other hand, can operate at extremely high speeds. It can cap hundreds of jars per minute, depending on the model. This high – speed operation allows jam manufacturers to significantly increase their production output, meeting the growing market demand more effectively.
Reduced Labor Costs
With the automation provided by the machine, the need for a large workforce to cap jars is eliminated. Instead of having multiple workers dedicated to the capping process, only a few operators are required to monitor the machine’s operation and handle any potential issues. This reduction in labor not only saves on wages but also reduces the risk of human error, such as misaligned caps or inconsistent sealing.
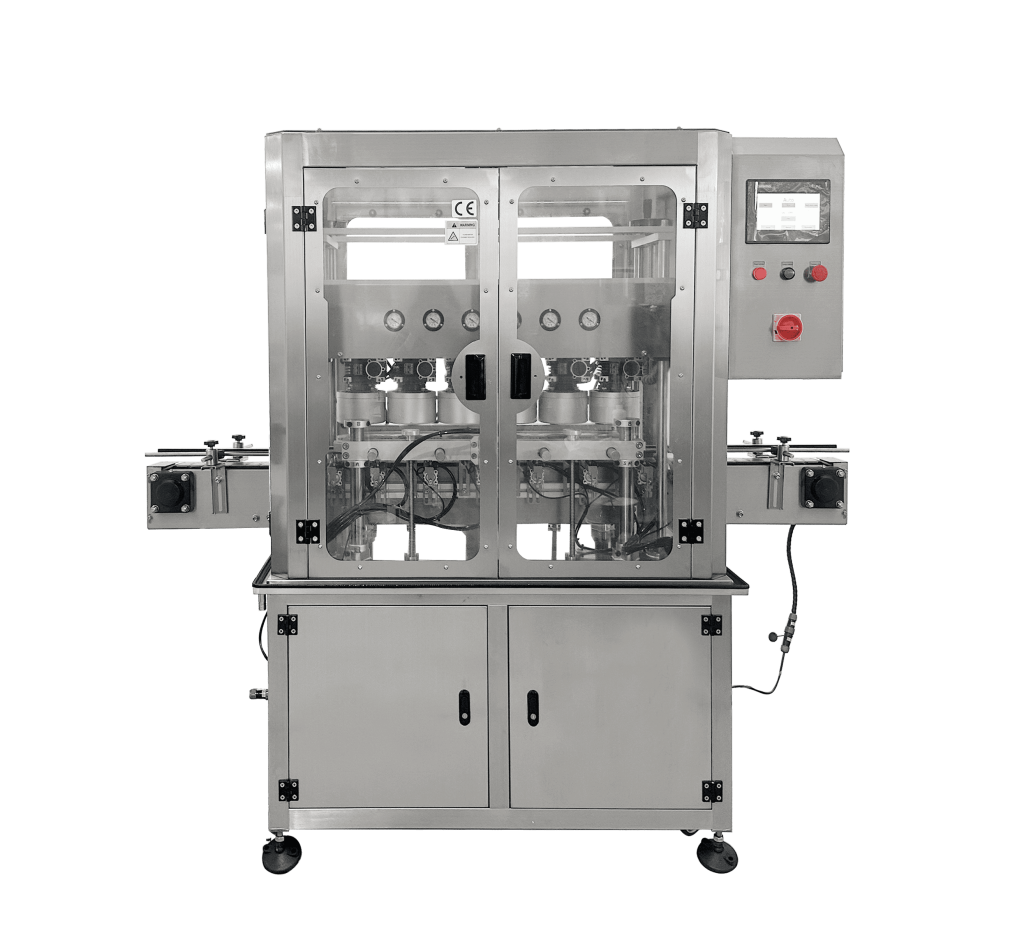
3. Consistent Packaging Quality
Uniform Sealing
One of the challenges in manual jam capping was achieving consistent sealing quality across all jars. Inconsistent sealing could lead to problems such as leaks, which not only wasted product but also damaged the brand’s reputation. The fully automatic vacuum capping machine applies a uniform amount of pressure and heat (if applicable) to each cap, ensuring a tight and reliable seal every time. This consistency in sealing is crucial for maintaining product integrity during storage and transportation.
Precise Cap Placement
The machine also ensures precise cap placement on the glass jars. It uses advanced sensors and mechanical systems to accurately position the caps, reducing the risk of misaligned or loose caps. This not only enhances the aesthetic appeal of the packaged product but also contributes to the overall quality and safety of the jam.
4. Hygiene and Safety
Minimized Human Contact
In the food industry, hygiene is of utmost importance. Manual capping involves direct human contact with the jars and caps, which can introduce contaminants such as bacteria, hair, or skin particles. The fully automatic jam glass jar vacuum capping machine minimizes human contact, reducing the risk of contamination. The machine is designed to handle the jars and caps in a controlled environment, ensuring a hygienic packaging process.
Safety Features
These machines are equipped with various safety features to protect operators. For example, they may have emergency stop buttons, safety guards, and sensors that detect abnormal operation. These features prevent accidents and injuries, creating a safer working environment for the production staff.
5. Adaptability and Customization
Compatibility with Different Jar Sizes and Shapes
The fully automatic jam glass jar vacuum capping machine is highly adaptable. It can be easily adjusted to accommodate different jar sizes and shapes, from small, single – serving jars to large, family – sized jars. This versatility allows jam manufacturers to diversify their product offerings and meet the changing preferences of consumers.
Customizable Sealing Options
The machine also offers customizable sealing options. Manufacturers can choose different types of caps, such as metal screw – on caps, plastic snap – on caps, or cork stoppers, depending on their product requirements and branding. Additionally, the machine can be programmed to adjust the vacuum level, sealing pressure, and other parameters to achieve the optimal sealing results for different types of jam.
Conclusion
The fully automatic jam glass jar vacuum capping machine has truly revolutionized the jam packaging industry. Its ability to enhance product preservation, increase production efficiency, ensure consistent packaging quality, maintain hygiene and safety, and offer adaptability and customization has made it an indispensable tool for jam manufacturers. As the demand for high – quality jam continues to grow, this machine will play an even more important role in the future of the industry.