In the realm of bottling operations, efficiency is the linchpin that holds together a successful production process. Single head servo control bottle screw capping machines have emerged as a revolutionary solution, offering a plethora of benefits that make them the key to achieving efficient bottling.
Table of Contents
Precision Engineering for Perfect Seals
At the heart of these capping machines lies servo motor technology. Unlike traditional capping methods, servo motors provide an unparalleled level of precision. They can be programmed to apply a specific amount of torque to each cap, ensuring a consistent and tight seal. This is crucial because a proper seal not only preserves the product’s integrity but also prevents leakage and contamination.
For example, in the pharmaceutical industry, where product safety is of utmost importance, a single head servo control capping machine can guarantee that each vial or bottle is sealed to the exact specifications. This precision reduces the risk of product spoilage and recalls, saving both time and money for the manufacturer.
Flexibility to Accommodate Diverse Products
One of the standout features of single head servo control capping machines is their remarkable flexibility. They can handle a wide range of bottle sizes, shapes, and cap types. Whether it’s a small, delicate perfume bottle or a large, industrial – sized container, these machines can adapt with ease.
This flexibility is a game – changer for businesses that produce multiple product lines. Instead of investing in separate capping machines for each product, a single machine can be used for all. This not only reduces capital expenditure but also saves valuable floor space in the production facility. Moreover, the ability to quickly switch between different bottle and cap combinations means that production can be more responsive to market demands.
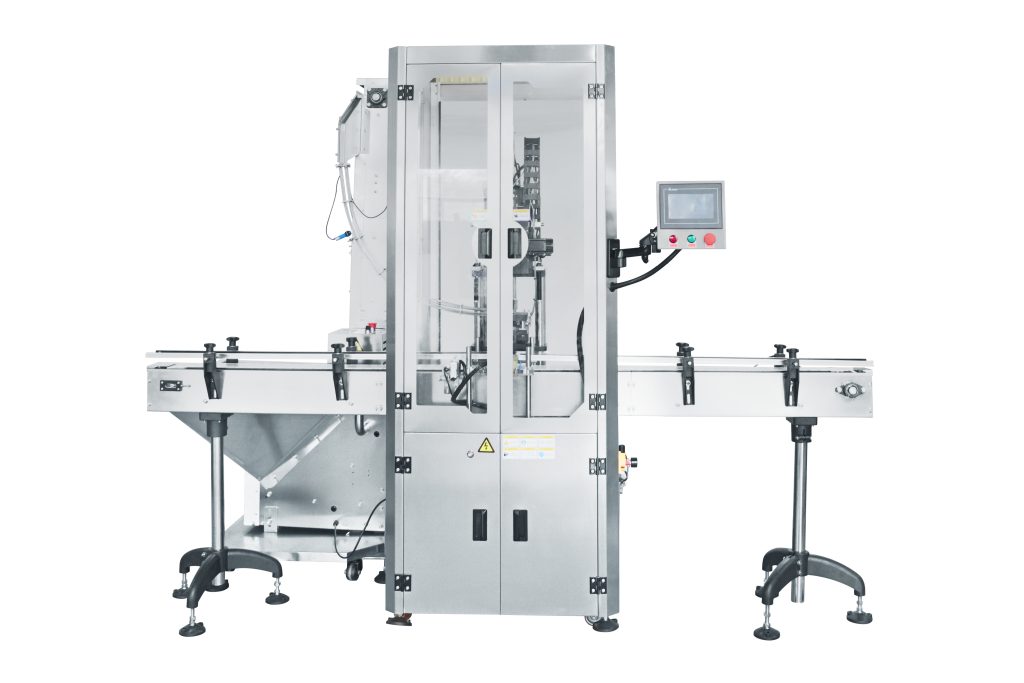
Streamlined Operations and Reduced Downtime
The design of single head servo control capping machines is focused on streamlining operations. They are equipped with user – friendly interfaces that allow operators to easily set up and adjust the capping parameters. Even those with limited technical knowledge can quickly learn how to operate these machines, reducing the need for extensive training.
In addition, these machines are built for reliability. The servo motor technology is known for its durability and low maintenance requirements. With fewer moving parts compared to traditional capping systems, there is less chance of mechanical failure. This results in reduced downtime for repairs and maintenance, allowing production to run smoothly and continuously.
Integration with Existing Production Lines
Another advantage of single head servo control capping machines is their ability to integrate seamlessly with existing bottling lines. They can be easily incorporated into a production process that includes filling, labeling, and other packaging operations. This integration ensures a smooth flow of products through the entire bottling line, eliminating bottlenecks and increasing overall efficiency.
For instance, the capping machine can be synchronized with the filling machine so that bottles are capped immediately after being filled. This not only speeds up the production process but also reduces the risk of product contamination during the transfer between machines.
Cost – Efficiency in the Long Run
While the initial investment in a single head servo control capping machine may be relatively high, the long – term cost – efficiency is undeniable. The precision and consistency of these machines lead to a significant reduction in product waste. Fewer bottles are discarded due to improper capping, which translates into cost savings on raw materials and production.
Furthermore, the energy – efficient nature of servo motors helps to lower operating costs. Over time, these savings can add up, making the machine a cost – effective choice for businesses of all sizes.
In conclusion, single head servo control bottle screw capping machines are the key to efficient bottling. Their precision, flexibility, streamlined operations, integration capabilities, and cost – efficiency make them an essential asset for any bottling facility. By investing in these machines, businesses can improve their production processes, enhance product quality, and gain a competitive edge in the market.